In the busy world of fixing cars, where medium-sized shops handle lots of orders every year, time is super important.
For every 1,000 car fixes, a shop might spend 333 to 500 hours dealing with paperwork, time that could be used to help the business grow.
Time is crucial in this industry, and that’s why many auto repair shops are turning to Automotive Repair Order Software. This tool not only streamlines order creation but also has the potential to boost overall revenue.
Before you decide to invest in auto repair order software, it’s crucial to fully grasp everything you need to know about it.
Within this guide, we’ll provide you with in-depth information about automotive repair order software.
Understanding Automotive Repair Order Software
The repair order is a written promise from a car expert (like a dealership or workshop) to a client who left their vehicle for fixing. It lists what parts will be changed and the tasks to be done. The expert needs to finish these tasks.
Businesses adopting auto repair order software may experience an average efficiency improvement of 15-20%.
Automotive Repair Order Software is a computer program designed to help car-related businesses, such as dealerships or repair shops, manage and streamline the process of creating, tracking, and completing repair orders. It assists in organizing information about the parts to be replaced and the tasks to be performed on a vehicle, making the overall repair process more efficient and organized.
Core functionalities
1. Work Order Creation and Management
Definition: The process of generating and organizing repair orders for each customer’s vehicle.
Key features:
i. User-friendly work order creation interface.
ii. Customizable fields for detailed job descriptions.
iii. Ability to attach images or documents related to the repair.
2. Customer and Vehicle Information Storage
Definition: Centralized storage of customer and vehicle data for easy access and reference.
Key features:
i. Customer database with contact details and history of services.
ii. Vehicle profiles with make, model, VIN, and maintenance history.
iii. Quick retrieval of customer information during service appointments.
3. Parts and Inventory Tracking
Definition: Monitoring and managing the availability and usage of auto parts and inventory.
Key features:
i. Real-time tracking of parts stock levels.
ii. Automated alerts for low inventory or reorder points.
iii. Integration with suppliers for seamless parts ordering.
4. Labor Tracking and Time Management
Definition: Recording and managing the time spent on each repair job by technicians.
Key features:
i. Clock-in/clock-out functionality for technicians.
ii. Job-specific time tracking for accurate labor cost calculation.
iii. Reporting tools to analyze labor efficiency.
5. Invoicing and Billing Capabilities
Definition: Generating invoices and managing the billing process for completed services.
Key features:
i. Automated invoice generation based on work orders.
ii. Integration with payment processing systems.
iii. Customizable invoice templates and detailed billing breakdowns.
Integration with Other Systems
1. Accounting Software
Definition: Seamless integration with accounting systems for financial management.
Key features:
i. Automatic synchronization of financial data.
ii. Quick generation of financial reports.
iii. Reduction of manual data entry errors.
2. Inventory Management
Definition: Coordinated tracking of inventory levels, reducing the risk of stockouts or overstocking.
Key features:
i. Real-time updates on inventory levels.
ii. Integration with suppliers for automated restocking.
iii. Reporting tools for inventory analysis and optimization.
Factors to Consider
Choosing an auto shop repair order software is a big step. If you are gonna invest in a digital tool, you must think about it carefully.
Following are some important factors that you need to consider before choosing an automotive repair order software:
1. Shop Size and Scale
Importance: The software should align with the size and scope of the automotive repair shop.
Considerations:
i. Scalability to accommodate future growth.
ii. Features tailored to the specific needs of small, medium, or large-scale operations.
iii. Customization options for a personalized experience.
2. Budget Constraints
Importance: Adhering to budget limitations is vital for the financial health of the business.
Considerations:
i. Upfront costs and subscription fees.
ii. Additional charges for updates or support.
iii. Comparative analysis of costs against features and benefits.
3. Ease of Use and User Interface
Importance: A user-friendly interface ensures smooth adoption and reduces training time.
Considerations:
i. Intuitive design for easy navigation.
ii. Comprehensive training and support resources.
iii. Accessibility for users with varying technical proficiency.
4. Compatibility with Existing Systems
Importance: Seamless integration with current tools and systems prevents disruptions and enhances workflow.
Considerations:
i. Compatibility with accounting software, inventory management, or other existing systems.
ii. Ease of data migration without loss or corruption.
iii. Minimization of potential conflicts between software solutions.
5. Mobile Accessibility
Importance: Mobile access allows flexibility and real-time management, particularly for on-the-go tasks.
Considerations:
i. Compatibility with various mobile devices and operating systems.
ii. Functionality and user interface consistency between desktop and mobile versions.
iii. Security measures for protecting sensitive information on mobile platforms.
Implementing Automotive Repair Order Software
Installation Process
The initial steps to set up and deploy the Automotive Repair Order Software (AROS) within the repair shop’s infrastructure.
Key Points:
a. Verify system requirements and compatibility.
b. Follow step-by-step installation instructions provided by the software vendor.
c. Conduct thorough testing to ensure proper installation and functionality.
d. Consider cloud-based options for simplified installations and updates.
Training Staff on Software Usage
The process of educating employees on how to effectively utilize the AROS for daily operations.
Key Points:
a. Offer comprehensive training sessions for all staff members involved in using the software.
b. Provide hands-on training with practical examples to reinforce learning.
c. Create training materials and documentation for reference.
d. Schedule follow-up sessions to address any questions or concerns.
Data Migration from Existing Systems
Transferring data from previous systems to the new AROS to maintain historical records and ensure continuity.
Key Points:
a. Conduct a thorough audit of existing data to identify what needs to be migrated.
b. Collaborate with the vendor of auto repair shop management software or IT professionals to
facilitate a smooth migration process.
c. Verify data integrity after migration and address any discrepancies promptly.
d. Implement a contingency plan to address potential data loss or corruption issues.
Troubleshooting and Customer Support Options
Establishing protocols to address issues that may arise during the implementation and usage of the AROS.
Key Points:
a. Document common issues and their solutions in a troubleshooting guide.
b. Provide multiple channels for customer support, such as phone, email, and live chat.
c. Consider implementing a ticketing system for efficient issue resolution.
d. Regularly update the software to address bugs and vulnerabilities.
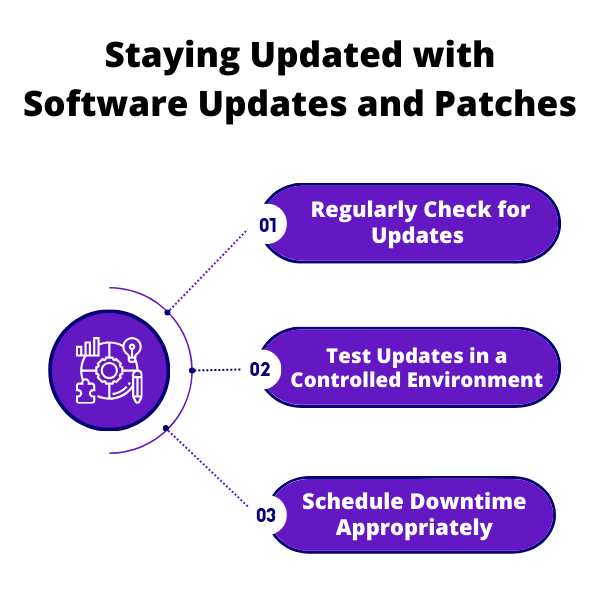
Maximizing the Benefits of AROS
Improving Efficiency and Productivity
AROS plays a pivotal role in streamlining internal processes, reducing manual tasks, and boosting overall operational efficiency.
Key strategies:
a. Automated work order creation and tracking to minimize paperwork.
b. Real-time updates on inventory levels, facilitating quicker parts procurement.
c. Time tracking features for accurate assessment of labor costs and job completion times.
d. Integration with scheduling tools to optimize technician workflow.
Enhancing Customer Experience
A positive customer experience is crucial for retention and word-of-mouth referrals, and AROS can contribute significantly.
Key strategies:
a. Quick access to customer and vehicle history for personalized service.
b. Automated appointment reminders and status updates for transparency.
c. Easy-to-understand invoices and billing breakdowns.
d. Integration with customer communication tools for seamless interactions.
Streamlining Communication Within the Shop
Efficient communication is essential for a well-coordinated repair process, from the front desk to the technicians.
Key strategies:
a. Centralized platform for sharing work orders, updates, and relevant information.
b. Real-time notifications and alerts for urgent tasks or changes.
c. Communication logs to track discussions and decisions regarding repairs.
d. Integration with messaging or collaboration tools for seamless communication.
Analyzing Data for Business Insights and Decision-Making
AROS generates valuable data that can be leveraged for strategic decision-making and business improvement.
Key strategies:
a. Reporting tools to analyze key performance indicators (KPIs) such as turnaround time and profitability.
b. Data-driven insights into popular services, customer preferences, and market trends.
c. Customizable dashboards for a quick overview of shop performance.
d. Integration with business intelligence tools for in-depth analysis.
Overcoming Challenges
Common Issues with AROS Implementation
1. Data Migration Problems:
Challenges in transferring existing data to the new system.
Solutions:
i. Thoroughly review data mapping and formatting requirements.
ii. Conduct trial migrations to identify and address potential issues.
iii. Seek assistance from software providers or experts if needed.
2. User Resistance and Training Issues:
Employees may resist adopting new software, leading to usability problems.
Solutions:
i. Provide comprehensive training sessions for all users.
ii. Create user-friendly guides and resources.
iii. Encourage a positive attitude toward the new system through incentives or recognition.
3. Integration Challenges with Existing Systems:
Difficulties in connecting AROS with other tools or software.
Solutions:
i. Choose software with robust integration capabilities.
ii. Work closely with IT professionals to address compatibility issues.
iii. Ensure thorough testing of integrations before full implementation.
4. Security Concerns:
Potential vulnerabilities leading to data breaches or unauthorized access.
Solutions:
i. Implement encryption protocols for sensitive data.
ii. Regularly update security measures to stay ahead of emerging threats.
iii. Educate staff on cybersecurity best practices.
Future Trends in Automotive Repair Order Software
Integration of AI and Machine Learning
The incorporation of Artificial Intelligence (AI) and Machine Learning (ML) into Automotive Repair Order Software for enhanced automation, predictive analysis, and decision-making capabilities.
Key Aspects:
a. Predictive Maintenance: AI algorithms analyze historical data to predict potential vehicle issues, enabling proactive maintenance.
b. Automated Diagnostics: Machine learning algorithms can assist in diagnosing complex vehicle problems based on patterns and data correlations.
c. Intelligent Scheduling: AI-driven scheduling algorithms optimize workflow by considering factors like technician availability, part availability, and job complexity.
Cloud-Based Solutions and Remote Accessibility
The shift towards cloud-based Automotive Repair Order Software, allows users to access and manage data remotely via the Internet.
Key Aspects:
a. Remote Management: Repair shop owners and managers can oversee operations and access data from anywhere, improving flexibility.
b. Data Security: Cloud solutions often include robust security measures, safeguarding sensitive customer and business information.
c. Collaboration and Integration: Cloud-based platforms facilitate seamless collaboration and integration with other cloud services and applications.
Emerging Technologies Shaping the Future of Automotive Repair Management
Exploration of cutting-edge technologies that have the potential to transform the landscape of automotive repair management.
Challenges and Considerations:
a. Implementation Costs: Adopting these technologies may involve initial investment and training costs.
b. Data Security and Privacy: As systems become more interconnected, ensuring the security and privacy of customer and business data is paramount.
c. Industry Adoption: Widespread adoption and acceptance of these technologies within the automotive repair industry may take time and require industry-wide collaboration.
Conclusion
And there you have it, the end of our Ultimate Guide on Automotive Repair Order Software!
Now, armed with the know-how, you’re ready to embrace the future of your repair shop.
Imagine less paperwork chaos, more satisfied customers, and a business that runs smoother than ever.
So, here’s to your shop’s future—may it be filled with innovation, happy repairs, and a dash of technological magic! Cheers to fixing cars the smart way!